Irwin Marine Services new pipe refurbishment, fabrication and re-coating workshop is now open in Shenzhen, servicing pan-China dockyards.
Attached is a short presentation on our refurbishment process.
In this case we were contacted on short notice by a superintendent that had a DN700 cooling system pipe that threatened to delay his vessel from leaving the dockyard. The China dockyard could not refurbish this pipe nor could it fabricate a new properly coated pipe in time to meet the deadline. Irwin Marine Services was given a 48 hour deadline to finish the job and we finished in 36 hours.
The owner also saved about USD 16,000 over the cost of renewing this pipe on a voyage repair basis by using our services and the refurbished pipe is better than the original.
We have already lined up a number of jobs to refurbish the cooling system pipes on a fleet of vessels with resulting savings to the owner of USD 20,000 to USD 30,000 per vessel.
Irwin Marine Services received this pipe on 8 May 2015 and was instructed to refurbish the pipe within 48 hours by the fleet superintendent.
The condition of the pipe as received was poor with the original rubber coating missing in most areas. A hole as well as heavy corrosion and pitting of the steel were observed.
We use a 10 hour burn off and cooling cycle where the pipe is heated to 440 degrees Celsius in a low oxygen environment. When the pipe is removed, all that is left of the old coating and paint is ash.
The pipe is ultrasonically tested for thickness to determine if the pipe is suitable for refurbishment. We follow ABS rules for minimum pipe thickness. In this case, the minimum pipe thickness, per ABS, was 6.3mm. Any location with thickness less than 6.3mm had to be built up by welding.
In addition to the some of the pipe walls that had to be built up by welding, all the joints for the branches and flanges also had to be re-welded and ground.
The interior of the pipe is grit blasted to white metal.
Notice some of the pits are more than 3mm deep. This pipe is not suitable for recoating via vulcanized rubber or epoxy coatings. Only rotational lining with a polyethylene (PE) coating is able to fill in the pits and crowns to create a smooth and long lasting coating.
The imported PE powder is added, the specially designed end caps are fixed in position and the pipe is turned in the coating oven to melt the PE to the interior of the pipe.
While in the oven, the pipe is turned in two axis to ensure even coating. Irwin Marine Services is the only company in China with a custom designed coating oven that is able to turn pipes of this weight. The DN 700 pipe weighed 807KG, the counter balance pipe weighed another 807KG for a total turning weight of 1614KG!
The end result is beautiful! The 6mm PE coating on the interior of the pipe has filled in all the pits and crowns with the result that the pipe is better than the original at a fraction of the cost of making a new coated pipe.
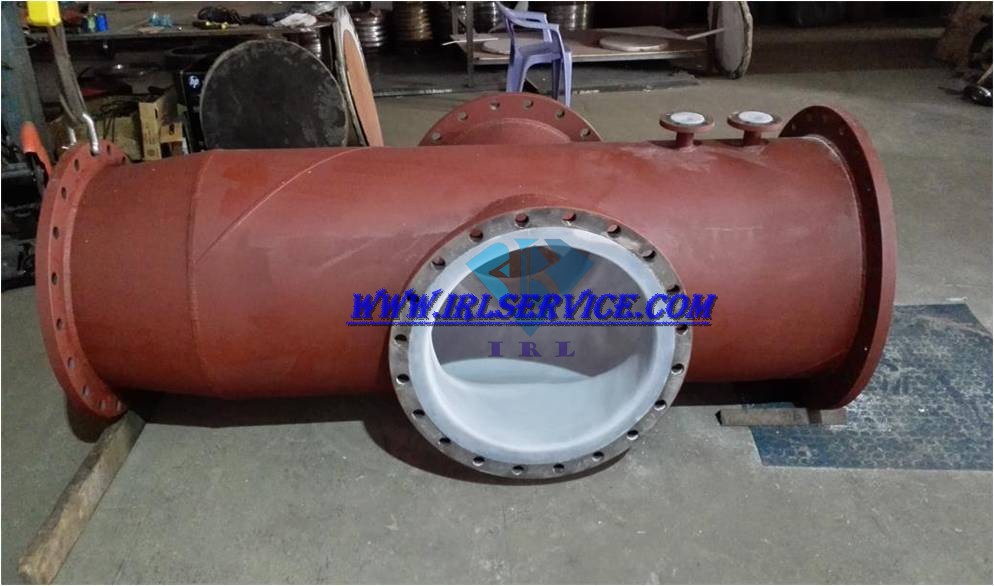
Note the smooth finish of the PE over the pitted surface after coating
The flanges are machined flat to a thickness of 2mm to ensure the old pipe will fit back into the original position. Korean shipyards (Samsung Heavy Industries) are using a similar PE coating applied by spray gun with a specification thickness of only 0.4mm. The 2mm thickness on the flanges exceeds the Korean standard by 500%. The 6mm coating on the interior exceeds the Korean standard by 1500%.
Following pressure test, end caps and a coat of primer are applied and the pipe is ready to return to the shipyard. In this case the pipe was completed in under 48 hours!